In Spring 2013 I was part of a 4-person team investigating the mechanical properties of 3D-Printed ABS plastic, in comparison to the mechanical properties of injection-molded ABS samples and machined ABS samples.
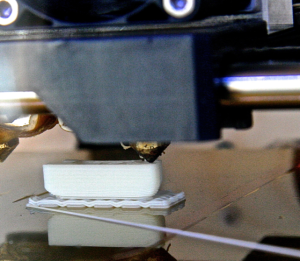
An example of a part being printed on an FDM Printer. The filament flows through the heated nozzle and the ABS fuses to create the final part.
Compared to injection molding and machining, 3D Printing is a newer manufacturing technology, primarily used for prototyping. It requires very little setup time since no molds or custom tools are needed. The most common 3D printers use a technique called Fused Deposition Modeling (FDM) for building parts layer by layer. A 2mm diameter filament is fed into a heating chamber where it is melted and forced out through a 0.4mm diameter nozzle, onto the build platform. The nozzle follows a computer-controlled path, building up the part from layers of small strands fused together as shown in Fig. 2. The resulting part is not completely solid, but is a matrix of fused filaments.
We were interested in looking at how three factors affect the strength and toughness of the 3D-Printed parts:
1) Orientation: Considering that 3D printed parts consist of filaments, the material is anisotropic. It is much weaker on the planes parallel to the layers than in other directions. For example, a shaft printed in a vertical orientation with many small round layers would be easy to snap, but the same part printed in a horizontal orientation with a few long layers would significantly less brittle. We tested samples printed in both orientations for our comparisons.
2) Print Density: 3D Printers can either print “solid” parts, where the volume is completely filled with layers of plastic, or “sparse” parts, where the outer surface of the part is solid but the interior is filled with a low-density honeycomb-like matrix. Sparse printing allows for increased speed and reduced usage of plastic for large parts. We tested samples printed in both densities for our comparisons.
3) Surface Treatment: Hobbyists have discovered that 3D printed parts can be given a smooth, shiny surface finish by immersing them in acetone vapor after printing, shown in Fig. 3. To do this, the part is hung inside a jar that contains a small amount of liquid acetone. The jar is then heated in order for the acetone to vaporize [3]. The use of acetone vapor over liquid acetone ensures a very consistent surface. The process achieves the smooth surface finish by softening the outer layer of plastic as the acetone breaks the secondary bonds between the ABS polymer chains. This allows chains to slide past each other and move to more stable positions. Surface tension in the liquid-like plastic layer polishes the surface texture, especially the small crevices between each successive layer. When the acetone evaporates, the plastic returns to its original hardness, but now has a well-bonded, continuous layer on the outer surface. We predicted that surface treatment with acetone vapor would increase the toughness of parts by improving the bonding between each of the layers.
RESULTS
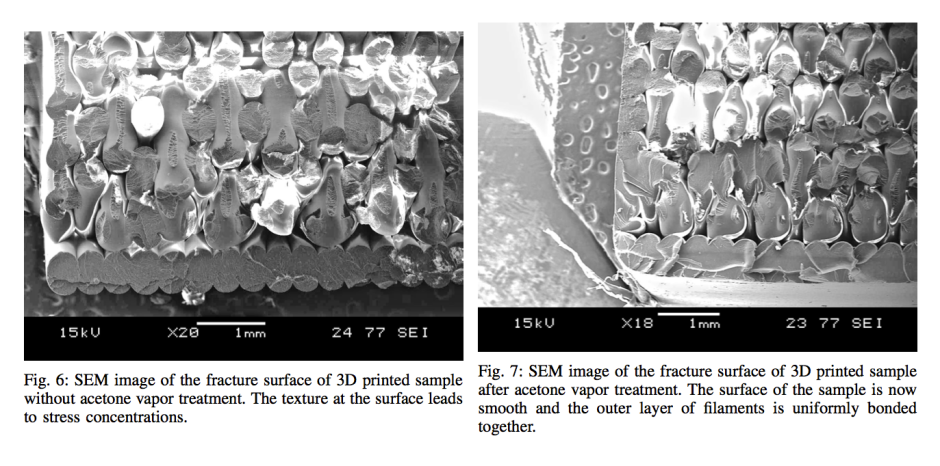
The sample without acetone treatment fractures filament by filament. There are very few crack propagation marks that cross filament boundaries. This indicates that the filaments are weakly bonded together instead of acting as a continuous piece of material. In comparison, the outer surface of the acetone sample has bonded into a continuous piece and crack propagation lines cross many filaments. The effect of the acetone is only visible on the perimeter filaments, indicating that the interior of the sample remains unchanged. The treatment process technically weakens the outer material by softening it, but the overall strength of the part increases due to the elimination of stress concentrations.
Within the context of low volume production, 3D printing orientation and printing resolution are important criteria due to their significance in determining the directional strength and cost of a part. In axial loading, parts printed with axially directed strands have favorable tensile strength and strain, while transverse strands are chosen to maximize part stiffness.
Additionally, post-treatment with part exposure to acetone vapor greatly improved strain, toughness, and surface finish in exchange for a small reduction in stiffness and tensile strength as a result of the melting and fusion of the ABS strands. It is therefore worth noting that if strain or toughness are the most important criterion then superior parts in both respects can be produced with both time and cost savings by reducing the 3D printing resolution and by acetone vapor surface treatment.
You can read our final report here: Final Report PDF
Hi Ben,
Very interesting, great work! Along the same idea, I was reading some of Steve Hernandez (https://github.com/Pacmanfan/UVDLPSlicerController) work developing 3D printers using a DLP projector to cure UV Resin, He used a regular filament 3D printer to build some of the parts for his DLP printer. He mentioned as incident where he accidentally spilled the UV resin on the some of his ABS parts and they started to dissolve (similar to acetone), to save his ABS parts he took them outside to let the sun cure the UV resin. His unconfirmed assessment of the new composite material was it appeared to be stronger the either component (ABS or UV resin) on its own. Are you up for another test?
Thanks,
Richard Applegate
Cool! Thanks Richard. I haven’t worked with that material but, but it would be fun to try out! On a side note, I’m curious how you happened upon my blog.
Hi Ben,
I saw the article on the squirrels and tried the acetone vapor bath on one of my ABS parts and suspected that the process might improve the part strength. I did a Google search and found your published paper and you, I don’t remember key words I used.
An inexpensive source for the UV resin: http://makerjuice.com/product-category/resins/
An interesting low cost STL printer concept: http://www.peachyprinter.com/#!methods/cjg9
Thanks for the quick reply,
Richard Applegate
Hi Ben, I saw the article on the squirrels and tried the acetone vapor bath on one of my ABS parts and suspected that the process might improve the part strength. I did a Google search and found your published paper and you, I don’t remember key words I used. An inexpensive source for the UV resin: http://makerjuice.com/product-category/resins/ An interesting low cost STL printer concept: http://www.peachyprinter.com/#!methods/cjg9 Thanks for the quick reply, Richard Applegate
________________________________